|
For selecting nozzles: Six required specifications
To select a suitable nozzle, it is necessary to have a set of at least six required specifications ready in advance. The following table, provided as an aid to understanding the terminology used in nozzle manufacturers product catalogs, lists these specifications and defines the meaning of each term. When you have understood the following terms, please establish your requirements for each one, then use the SGS Free Trial and see if the SGS can identify nozzles meeting your specifications.
Pressure | Flow rate
| Spray angle and Spray width | Spray pattern
| Material of manufacture | Connection type
 Pressure
In most manufacturers' product
catalogs, the word pressure indicates
the pressure of fluids near the
point where the fluids flow into
the nozzle (the inlet). If, for
example, the pressure gauge is some
distance from the nozzle, the reading
on the pressure gauge will not accurately
reflect the actual fluid pressure
at the nozzle. Similarly, if the
pump is too far away from the nozzle,
or if the potential head difference
is too great (i.e. the pump is much
lower than the nozzle), it may not
be possible to able to obtain the
designated flow rate. Therefore,
nozzle pressure, in general
refers to the pressure at the inlet
(please see the following illustration).
Moreover, pressure can be measured
in MPa, PSI, BAR,
etc., so manufacturers give pressure
values in different units. (The
SGS Unit
Converter enables you to convert
values into your preferred units
quickly and easily.)
 Flow rate
Flow rate is the amount of liquid sprayed from a nozzle's orifice per hour. In principle, the required flow rate will depend upon the application and the purpose for which the fluid is being sprayed. It is important to be aware, however, that clogging can occur inside the nozzle if foreign matter is present in the material being sprayed. Most nozzle manufacturers give the free passage diameter as well as the orifice diameter of their nozzles in their product catalogs, which is helpful. Flow rate is usually calculated from the orifice diameter (cross-sectional area) and pressure, so a bigger orifice and lower pressure (theoretically) produces the same flow rate as a smaller orifice and higher pressure. (Please refer to the formula below.)
Flow rate formula:
The SGS Unit
Converter enables you to make
these calculations easily.
According to the formula above, the flow rate of a nozzle is proportional to the square root of pressure.
N.B. When a liquid whose viscosity
or density differs from that of water
is to be sprayed, the actual flow
rate may not match that given for
the nozzle in the manufacturer's catalog.
(The SGS Unit
Converter enables you to easily
convert density values relating to
flow rate into your preferred units.)
 Spray angle and Spray width
Spray angle refers to the angle at which the sprayed fluid fans out from the nozzle. Spray width represents the width/diameter to which the sprayed fluid has fanned out at a predetermined distance from the orifice. When a nozzle is positioned to spray downwards, the spray width actually tapers off as the distance from the orifice increases (like a candle flame). Therefore, the theoretical spray width that may be obtained based on the spray angle value given for a nozzle in the manufacturer's catalog may not match the actual spray width. If a spray distance of several meters is required, the manufacturer's advice should be sought.
Although, in general, the spray angle produced by a particular nozzle varies according to pressure, most manufacturers' product catalogs show spray angles at each pressure value. The following graph shows the relationship between pressure and spray angle of flat and full cone type nozzles.
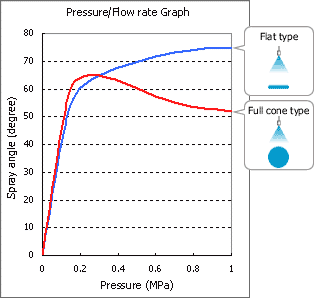
 Spray pattern
Spray pattern refers to a cross-section of the main body of sprayed fluid as it disperses. Patterns can be circular, bar-shaped etc. Spray pattern names can be classified as the table below shows. (Please note that spray pattern names used in manufacturer's product catalogs are not standardized.) In principle, nozzle users themselves have to choose a spray pattern to suit their application or purpose. A nozzle manufacturer's advice may be sought to aid in decision-making.
Universal Nozzle Spray patterns |

Nozzle produces a dot-shaped spray pattern on the target surface. |

Nozzle produces a solid, circular spray pattern on the target surface (full cone). |

Nozzle produces a hollow, circular, ring-shaped spray pattern on the target surface (hollow cone). |

Nozzle produces an oval spray pattern on the target surface (oval full cone). |

Nozzle produces a square-shaped spray pattern on the target surface (square full cone). |

Nozzle produces a flat, bar-shaped spray pattern on the target surface. |

Nozzle discharges tangentially and produces a solid, circular spray pattern on the target surface (full cone). |

Nozzle discharges tangentially and produces a hollow, circular, ring-shaped spray pattern on the target surface (hollow cone). |

Nozzle discharges tangentially and produces a bar-shaped spray pattern on the target surface. |

Nozzle discharges tangentially and produces a dot-shaped spray pattern on the target surface. |

Nozzle is equipped with multi-orifice, which produces solid stream. |

Nozzle produces a long, narrow, spray pattern. (A slit-shaped orifice discharges a curtain of fluid). |

Multiple orifices produce a full cone spray pattern. |

A double or triple spiral spray pattern is produced on the target surface. |
|
 Material of manufacture
Nozzles are generally made of such materials as brass, stainless steel, or plastic. When choosing a nozzle it is necessary to select a material of manufacture that suits the application to which the nozzle will be put. Brass is the easiest material for nozzle manufacturers to work with and is a common material, but brass nozzles have insufficient resistance to abrasion at middle/high pressure, and limited resistance to corrosion by corrosive chemicals. Due to its relatively high abrasion and corrosion resistance, stainless steel is widely employed in nozzle manufacture, SUS303 stainless steel being the favored grade of this material. When the liquid to be sprayed or the surrounding atmosphere is corrosive however, nozzles made of SUS316 or SUS31L stainless steel, both of which have superior resistance to corrosion, are more suitable. Relatively few types of nozzles are manufactured from plastic, thus limiting the number of models available. Plastic nozzles are useful for spraying chemicals that corrode metal nozzles too quickly.
Tungsten carbide nozzles can withstand high pressure, and ceramic nozzles have high abrasion and corrosion resistance. Types of material and model numbers indicating material of manufacture are shown in nozzle manufacturers' product catalogs.
 Connection type
The most common means of fitting a nozzle to a supply pipe is by screw thread, but nozzles that are required to deliver high volumes of liquid are often fitted with flange connectors. Essentially, manufacturers determine nozzle connection types and diameters according to flow rate and configuration. These details and dimensions are shown in their product catalogs, accompanied by corresponding model numbers. Detailed dimensions of threads and flanges differ from country to country owing to differing industrial standards, so, when ordering products manufactured by overseas suppliers, please take care that dimensions, threads etc. are compatible with the system into which they will be introduced.
|